Education

Quality education is essential to a skilled and competitive workforce. Access to education, coupled with reliable, quality childcare is key for improving economic opportunities for all Americans.
Our education system is failing many students as shown by data that reveals two-thirds of our fourth and eighth graders are unable to read or do math at their grade level. And the United States ranks below a number of other countries in reading and math proficiency. Recognizing the importance of childcare as a key component of the education system is crucial to addressing the current challenges and ensuring that every child has the support they need to thrive.
- 6th in ReadingGlobal Ranking for U.S. Students
- 10th in ScienceGlobal Ranking for U.S. Students
- 26th in MathGlobal Ranking for U.S. Students
How can the U.S. be competitive without math? This is the question that America’s business leaders need to be asking themselves as we receive yet another concerning indicator that our nation’s public education system is moving in the wrong direction.
Opinion
U.S. Chamber Foundation Senior Director Aaron Merchen argues that employers are increasingly recognizing that child care support is vital to not only help businesses survive but also to help communities thrive.
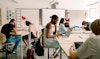
Future of Data in K-12 Education Initiative Can Help Inform a Critical Impasse
The U.S. Chamber Foundation has launched a multi-year initiative with the support of a working group of preeminent leaders in education to develop policy recommendations focused on all students, especially those who have been historically underserved by the K-12 system.
Learn More
Bridging the Education-Workforce Gap
Despite the constant evolution of the job market, educational curricula often lag, inadequately preparing students for the real-world challenges they’ll face in their careers.
Programs
Latest Content
Columbus Area Chamber president and Business Leads Fellow, Dawson Brunswick, navigates tomorrow's workforce woes today, weaving education, childcare, and community engagement into a brighter future.
Dive deeper with Joseph Davis and Sydney Lewis as they debunk the most common childcare myths, inviting you to explore the hidden truths that every American family should know.
Sasha Nicholas, associate manager of early childhood education, reflects on key takeaways from the panel, "Piecing Together Childcare Solutions," an engaging conversation held at the 14th Annual International Women's Day Forum.
Barbi Jones is moving North Carolina forward in her role as executive director of the Cabarrus Regional Chamber of Commerce, and as a Business Leads Fellow.
Elise Awwad, President and CEO of DeVry University, is a lifelong learner and passionate leader, championing education as a tool for challenging societal norms and achieving economic mobility, especially for women.
“What do you want to be when you grow up?” might be a question asked of children, whose dreams and aspirations can feel far-fetched and far-reaching in ways that inspire and humor us. But as those children grow into young adults, navigating the pressures, stressors, and opportunities that come with making decisions about the future, we believe career readiness can do more to support young people as they decide what they’ll grow up to be—and give them the resources and tools to do it.
How can the U.S. be competitive without math? This is the question that America’s business leaders need to be asking themselves as we receive yet another concerning indicator that our nation’s public education system is moving in the wrong direction.
Zeb Welborn and Renay Sehgal Mehta, through their roles at the Chino Valley Chamber of Commerce and as Business Leads Fellows, are tackling workforce shortages facing businesses and communities.
Dr. Timothy Magner, president of the Greater Shreveport Chamber of Commerce, uplifts communities through connecting business and education, and championing collaboration as a Business Leads Fellow.